Our Process
How is Lumin plywood produced?
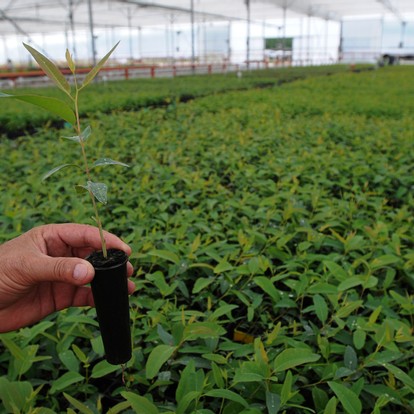
Planting
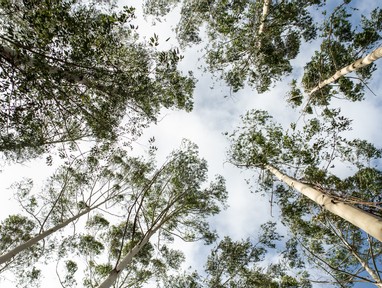
In our nursery we produce eucalyptus and pine seedlings, which will be planted and managed with pruning and thinning for the production of high-quality wood
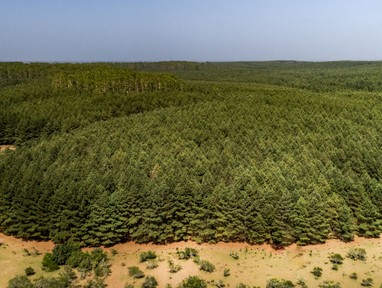
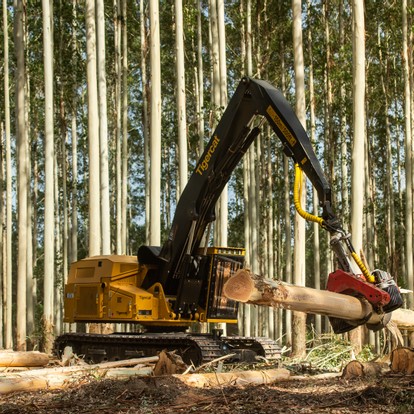
Harvesting
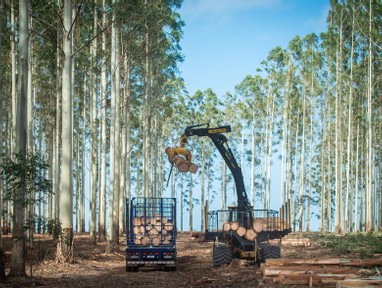
We harvest following an operational plan that contemplates the industry needs and the maximization of our forests
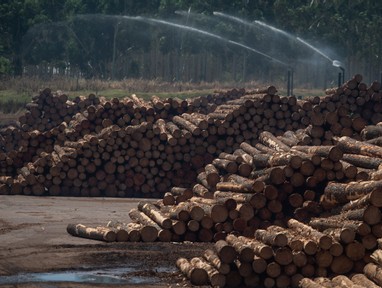
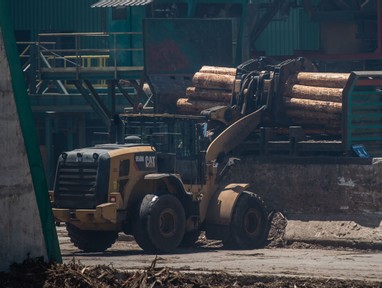
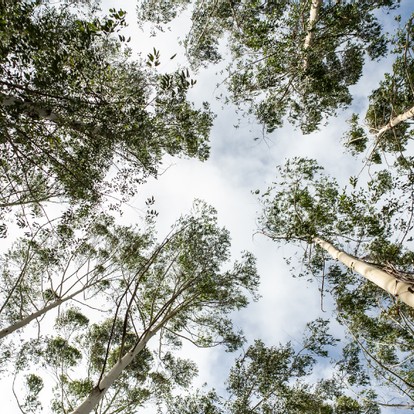
Debarking
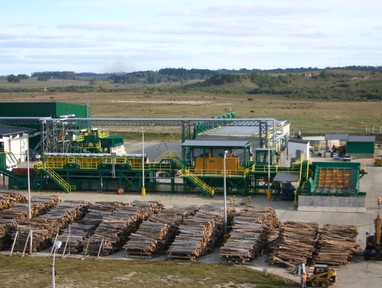
The goal for this process is to remove the bark from the trunk without causing damage to the wooden rolls.
To do this, front loaders with grapes are used to remove the rolls from wet storage piles and feed them to a ring debarker. The debarked pieces are then organized by size and diameter before the next stage.
The bark that was removed by this equipment is fed, through a mechanical conveyor, to a shredder in order to reduce its size so it can be used as solid fuel for steam generation.
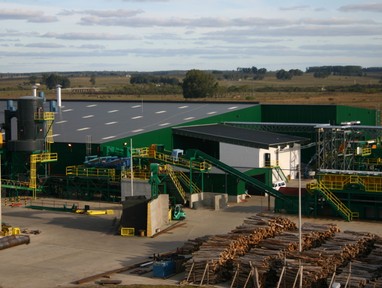
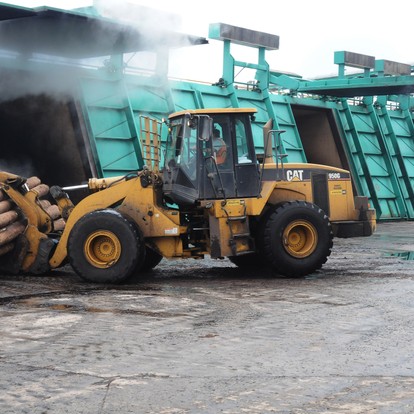
Conditioning
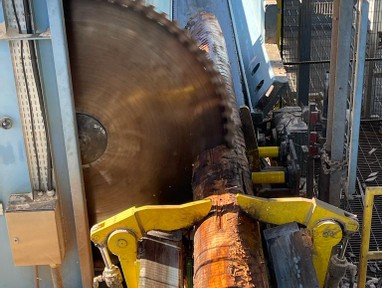
The debarked rolls are removed with front loaders from the forestry hoppers, where they've been stored after the previous stage, and placed in vaulted chambers for double and single length rolls, in parallel for their conditioning.
The goal of this step is to soften the rolls' fibers so that further steps can be easier.
The hot water raining over the rolls warms them up, and at the same time runs between them like a waterfall, until it reaches the floor of the vault sliding towards the back.
Trimming saws
Once conditioned, with the help of front loaders, the rolls are removed from the maceration chambers and fed to a saw system that trims them (Bucking) to get pieces with an uniform length of 2.63 m each, known as logs. This operation is carried out in two production lines, each of them equipped with 3 circular saws. They're then moved to the turnstile of the corresponding line through a conveyor belt.
The wooden tips that result from these cuts on the rolls to take them to a decoilable (trimmed) size, are minced in chippers, and through a conveyor belt system are led to the wood waste deposit to be used as solid fuel for generating steam and electric power.
The logs that for some reason don't meet the production process' requirements are sent to a rejection bin, where they can then be minced and turned into fuel, or returned to the supplier.
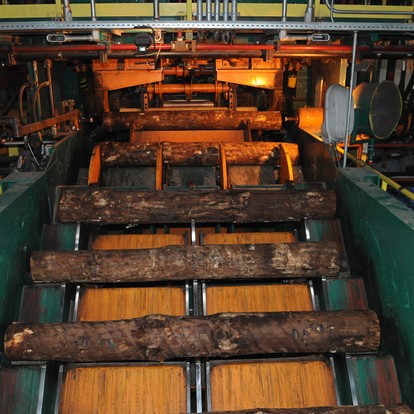
Decoiling
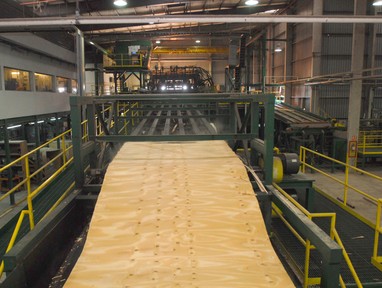
Lathes (3 lines of decoiling, 8’)
The logs that come from the trimming saws are piled in their respective collection tables and lifted though a feeder that moves the logs one by one to the lathes' XY loader. The XY loader includes several laser sensors, that recognize the shape of every log and make it rotate once (360°) over two fixing points. After recon, the two fixing points are placed so that when the log is placed in the lathe's rotation axes, maximum capitalization on this wood can be obtained by decoiling.
When the blade is placed over the spinning log, a thin wooden sheet of the desired thickness is decoiled.
Once the logs have been peeled, what's left is their knobby cylindrical core. This core will be used in several by-products, including separator slats for the sheets and for packaging the laminated wood panels or, alternatively, to make pallets or be fed to a shredder to make chips for steam generation fuel.
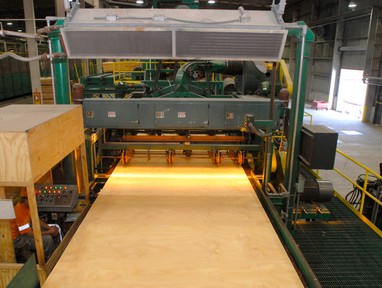
Clipping and stacking
The continuous wooden sheet coming from the lathe (veneer) is analized by a scanner in order to find faults, knobs or breakages in that veneer piece. The system is made up of a camera, a light source that allows for a continuous analysis of the veneer moving below it, a guillotine (Rotary Clipper), and control software that commands the guillotine and cuts the veneer sheet according to the analysis results.
When the scanner finds some kid of defect on the sheet moving underneath it, it will command the guillotine to make a cut before and after the defect, thereby making sheets of smaller sizes. Depending on the resulting length, they will be called half a sheet if they're at least 0.7m long, and random if they're below that length. These smaller pieces are then moved to a manual classification table, where operators organize them by quality and width.
These sheets and strips piled manually and automatically, are transported through forklifts to the wet sheet deposit area (Wet Veneers).
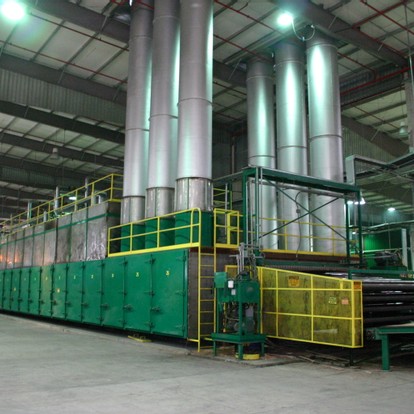
Drying
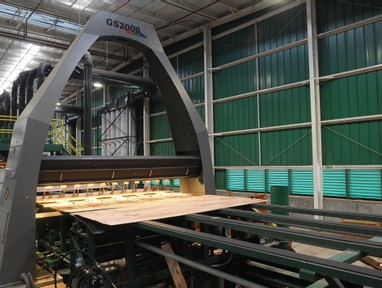
The trimmed veneer sheets, whether full, half or random size, enter the drying process in parallel, heated by indirect steam with the goal of reducing their humidity content.
It's generally reduced by a relatively wide range of percentages, between 4% and 15%. The horizontal drying of sheets is characterized by air circulation parallel to the sheets, or by directing hot jets of air at high speed to the surface of the sheets creating a more turbulent air flow. This allows for a more efficient energy use of the dryer by reducing the drying time. Once dry, they go through a humidity detector based on the sheet's quality and humidity content, and are classified according to the desired requirements.
They're then relocated to the dry sheet storage area. If they're not at the desired humidity, they re-enter one of the dryers at a lower temperature to complete the required drying process (redrying process).
Sheet composition (composers)
To make use of the strips or randoms, there's specific equipment (Core Composers) with the purpose of preparing full-size sheets from pieces with defined length and width. The machine holds a straight edge cut with the right blades over the narrow pieces of wooden sheet, places glue and joins the strips to form full-size sheets that are then mechanically clutched and cut in the required size.
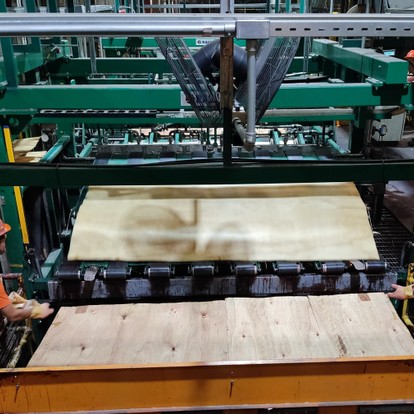
Adhering

Panel queuing and assembly
Dry wooden sheets, stored in their corresponding deposit area, are relocated through forklifts to an automated board assembly line, with adhesive application through extrusion.
This equipment's goal is to evenly distribute or apply adhesive. The queued sheets from the cores are assembled with the sheets for the faces to give way to the wooden panels.
The assembly of the wooden panels must be symmetrical on both sides of the core to avoid excessive warping.
Adhesive
The phenol-formaldehyde required for the process is supplied by an external distributor, ready to use. This allows for the produced panels to be exterior resistant and compliant with the product certifications mentioned in our website.
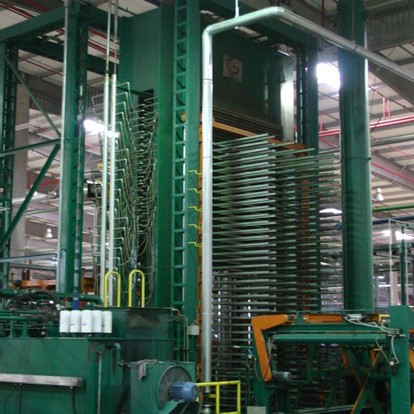
Pressing
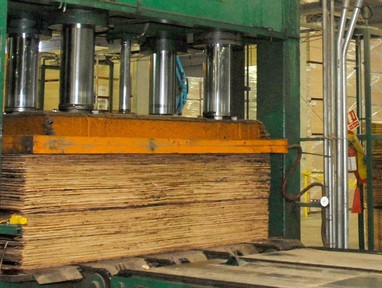
The packages of queued and assembled sheets are loaded in the installed Pre-Presses before entering the Hot Presses.
Each Pre-Press applies enough pressure to join together the sheets making up the panels, so these panels can then be separated, manipulated or placed individually by the Hot Press.
Each Hot Press applies pressure and heat to the panels to set the adhesive's resin and join together each panel's sheets. The hot pressing has two main goals: spreading the resin so it's a thin layer over each wooden sheet and activate its thermal setting.
The pressing time and temperature can vary according to the type of wood and the board's thickness.
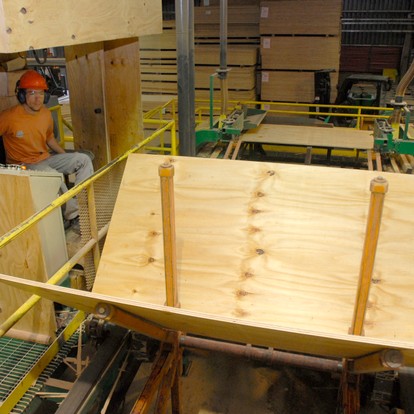
Sanding

Finishing operations. Squaring, repairing, sanding and classification
The laminated wooden panels are, at last, put though a finishing process where the edges are cut and the exterior faces can be sanded to give them a soft final touch. The type of finish depends on the final product that's been aimed for to meet the market's demands.
Once the panels' dimensions have been adjusted, they go though ultrasound equipment (Blow Detector) that verifies the perfect adhesion of every layer in the panel. Next, a qualified operator inspects and defines (classifies) the grading for every panel. The panels are then automatically piled according to their quality grade.
As a result of this quality control, some of the panels are sent to a repair line (Poly Patch) that allows for their quality to be improved by filling certain imperfections and knots with specific and certified chemical products.
The panels then continue their finishing process by moving to the Sanding section, where the panels' faces are sanded until they reach the desired finish.
The work stations for each of these finishing operations include dust extraction systems to capture the fine dust that's generated in the process to ensure a satisfactory work environment, and that subproduct is then sent to be used as boiler fuel.
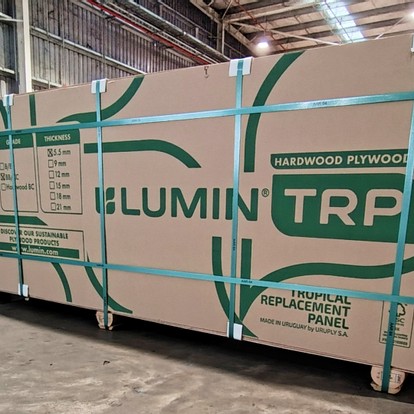
Grading and packaging
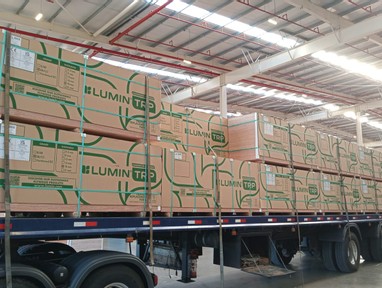
The board packages, after the last step of the process, get prepared for storage and delivery according to their destination, final customer and quality grading.
They can be processed with different kinds of packaging: film stretch, the sides of the package painted in the corresponding chamber, or plastic straps, depending on their quality grading, destination or final customer.
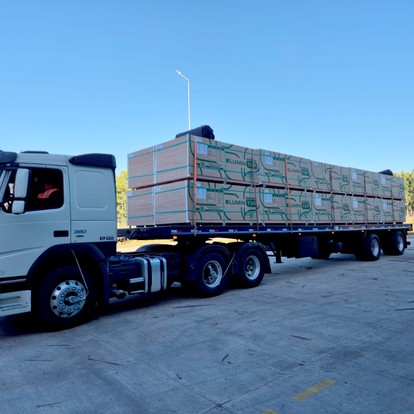
Transportation
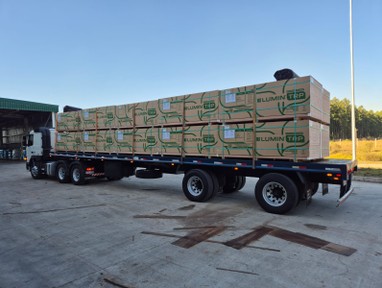
The board or sheet packages can be sent from the Plant though railway transport or truck, also depending on the market, client or final destination.